Testing Wet Adhesion Properties of Interior Architectural Coatings
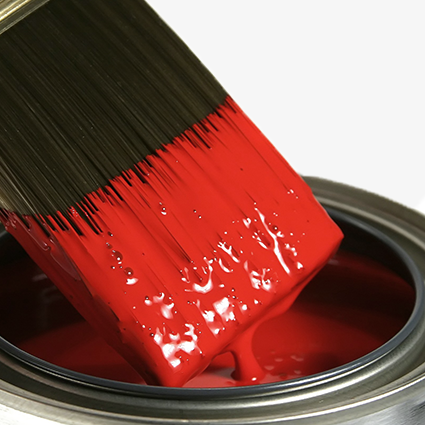
Testing Wet Adhesion Properties of Interior Architectural Coatings
While scrub resistance is the ability of a paint surface to resist wear when rubbed with a brush, sponge or cloth, and washability is the ability to remove stains from the surface with little wear, wet adhesion is the ability of a paint to stick to alkyds (oil-based) paints.
ASTM Testing to Measure Scrub Resistance of Wall Paints
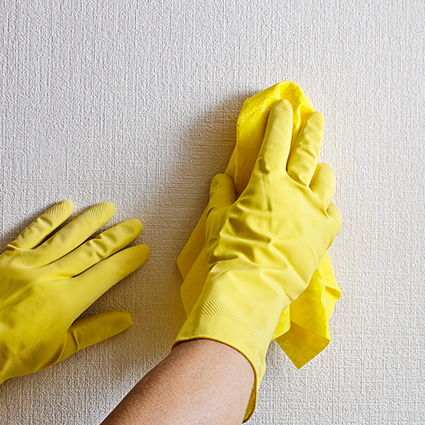
ASTM Testing to Measure Scrub Resistance of Wall Paints
Waterborne architectural coatings are expected to deliver a high level of performance. Considering that these films are at most a few thousandths of an inch, these coatings are incredibly resilient. Over the next couple months we will compare and contrast a few related but significantly different tests for interior coatings. The first test we will discuss is abrasive durability.
A must-have performance characteristic of any interior waterborne architectural coating is scrub resistance. Scrub resistance is the ability of a paint surface to resist wear when rubbed with a brush, sponge or cloth. A coating with good scrub resistance protects the substrate, mitigating exposure and damage, and maintaining aesthetics among other properties. A paint’s ability to be scrub resistant is especially important in high traffic places like play areas and around doorways and windows.
At 1st Source, ASTM D2486 (Standard Test Methods for Scrub Resistance of Wall Paints) is routinely used for testing paints. Testing using ASTM D2486 requires appropriate controls and coating thickness. The use of a constant temperature/constant humidity room ensures consistent drying conditions for all tests. Appropriate substrates, conditioning of the scrub brushes and the type of abrasive scrub media are specified. Coatings that provide the highest number of scrub cycles before wear through are considered superior to others from a durability perspective.
A related test is the washability test; the ability of coatings to release stains. We will discuss it in more detail next month and contrast it to scrub resistance.
Fire Protection of Building Structures with Intumescent Coatings
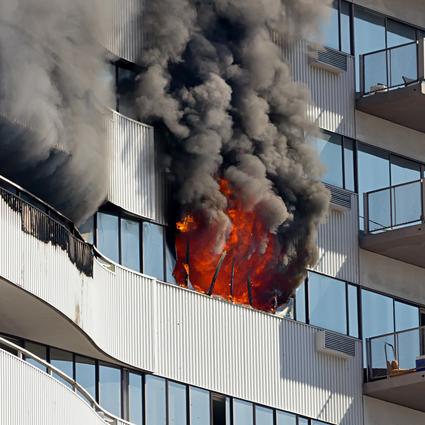
Fire Protection of Building Structures with Intumescent Coatings
When exposed to fire, building materials lose integrity. Concrete can spall and crack exposing rebar, which can lead to structural failure. Wood is easily charred and will quickly loose structural integrity. Steel will start to lose strength at 400 °C.
There are two main methods of fire protection, active and passive. Active protection systems are typically sprinklers and alarms, while passive fire protection (PFP) systems perform without an external trigger.
PFP enables owners to protect the strength of steelwork and slow the spread of fire, increasing the length of time for escape. Most PFP systems require minimal operation maintenance and last the lifetime of the structure. One category of PFP is called an intumescent coating. When these coatings are exposed to fire, the coating increases in volume (intumesces) up to 50 times its original size producing an insulative layer, reducing the heat transfer to what it is covering.
Fire protection of buildings using intumescent coatings is a critical and growing market. According to a report by Grand View Research, the market will reach $1.31 billion by 2025. Over the next couple of months, we will discuss this important market with respect to size, profitability, available technology, and innovation trends.
Impact Modifiers
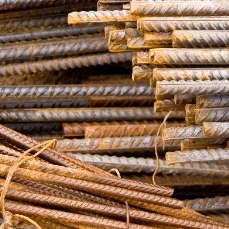
Impact Modifiers
Current U.S. Federal Highway Administration’s cost on the loss of infrastructure due to paint and coatings failure is estimated at over 1 trillion dollars. In order to combat this, according to Bloomberg (April 20, 2017), the current administration wants a trillion dollars’ worth of infrastructure work on the ground. Two hundred billion dollars will come directly from the government. This will be applied to roads, airports and other public works, of which improved impact of epoxy coatings will play a part.
Ongoing government legislation and consumer demand also requires the reduction of solvents (VOCs) in epoxy coatings. Coating manufacturers must find alternate products that lower viscosity, provide impact and flexibility, and improved hydrophobicity, while simultaneously lowering the overall cost and carbon footprint of epoxy coatings.
Stop by the 1st Source booth #423, at the Western Coatings Symposium in Las Vegas, (Oct 15th to 18th) and learn how we can help you develop low cost epoxy modifiers for your application that will help you reach your performance goals. Testing includes corrosion resistance, viscosity, flexibility, impact resistance, tensile, adhesion, abrasion and gloss among many others.
1st Source Research has a strong coatings team that allows us to combine these techniques with other sophisticated analytical tools to diagnose paint quality problems, validate raw materials, and optimize processes that may be holding you back. Feel free to contact us. We’ll be happy to lend our expertise and analysis techniques to help you meet your goals.
Redox for Main Polymerization of Emulsion Polymers
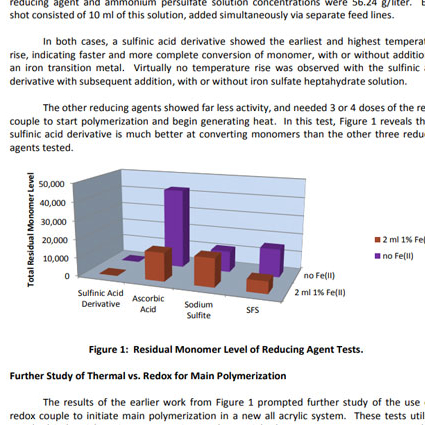
Redox for Main Polymerization of Emulsion Polymers
Going from Strength to Strength
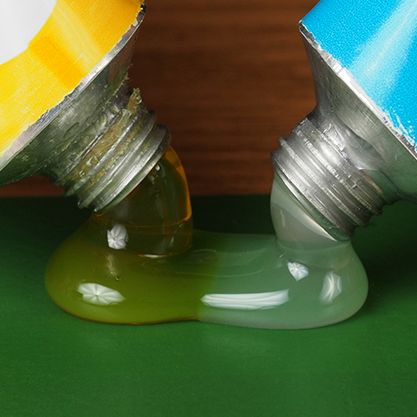
Going from Strength to Strength
European Coatings Journal publishes technical paper authored by 1st Source Research CEO, Gerald Vandezande. In “Going from Strength to Strength” Vandezande describes how a new additive improves performance in several key properties. A new type of additive has been developed with the aim of enhancing several key properties of two-pack epoxies simultaneously. Flexibility, adhesion and corrosion resistance were all found to be improved. Some benefits could be obtained in the pot life to cure speed ratio. Click here for the technical paper.
Coatings Industry Innovation
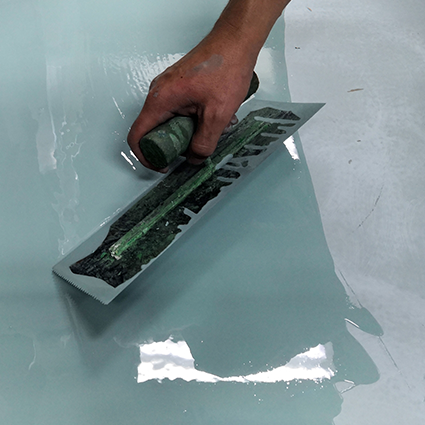
Coatings Industry Innovation
The coatings industry is continually innovating to produce products with lower VOCs while maintaining properties and productivity. This is particularly true for the Maintenance and Marine markets where solvent borne or 100% solids epoxies are used to impart excellent protective properties to valuable steel and concrete substrates.
Reducing VOCs in epoxy coatings are particularly challenging since the reduction of solvents generally leads to significant viscosity increases. This increase causes difficulty in mixing and application of these two component systems. In order to counteract this problem, lower viscosity, lower molecular weight resins are employed. This in turn embrittles the final epoxy coatings reducing impact resistance and flexibility. These epoxies also contain higher levels of functional groups requiring more of the costly hardener to cure. This not only increases costs but also increases the latent heat of the system greatly reducing the workable pot life.
In subsequent posts, we will report on a new breakthrough technologies that improves the impact resistance and flexibility of low VOC epoxy systems while maintaining surface hardness. Simultaneously pot life, gloss, and corrosion resistance are substantially improved.
Epoxy Coatings Properties and Market Needs
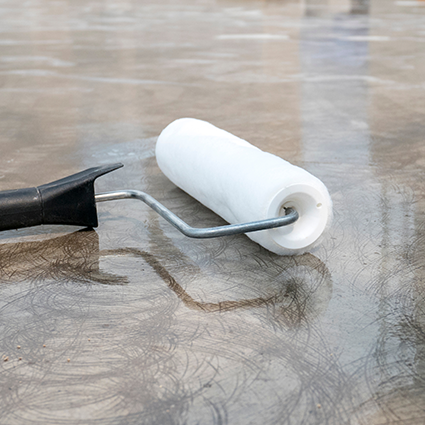
Epoxy Coatings Properties and Market Needs
Epoxy coatings are expected to have the following properties: resistance to a wide variety of chemicals, outstanding corrosion resistance, and adhesion to a wide variety of substrates including marginally prepared metal surfaces and concrete.
When developing new additive for the epoxy coatings market, it is important to keep in mind that any added ingredient can enhance performance in one area while detracting from performance in another. Also, current high performing products can be quite complex and adding a further new ingredient increases the complexity even more. A good additive will address or target multiple aspects of an epoxy coating and strive to improve or replace two or three properties simultaneously in order to add value to the new raw material and reduce the complexity of existing formulations.
Currently there are separate raw materials used to enhance adhesion to various substrates, improve corrosion resistance, aid in improving impact and bend properties, as well as improving gloss for aesthetic purposes. These ingredients often do not complement each other. For instance, adding low molecular weight low viscosity mono functional epoxies can increase flexibility but reduce adhesion. Still other additives are used to lengthen pot life and shorten cure time, especially in cold weather, but this comes at the cost of color and toxicity. A current trend in the industry is to reduce VOC levels without impacting any other properties of a coating. In addition to this, the market is requiring thinner coats while maintaining performance.
Reducing VOCs in epoxy coatings is particularly challenging since the reduction of solvents generally leads to significant viscosity increases. This increase causes difficulty in mixing and application of these two component systems. In order to counteract this problem, lower viscosity, lower molecular weight resins are employed. These require more hardener to build molecular weight and cure, and the additional crosslinking in turn embrittles the final epoxy coatings reducing impact resistance and flexibility among other properties. These epoxies also contain higher levels of functional groups requiring more of the costly hardener to cure. This not only increases costs but also increases the latent heat of the system greatly reducing the workable pot life.
To this end, an ambitious project was undertaken to develop a single multifunctional additive, allowing the removal of existing additives and enhancing the final product performance. The base formulation was to be a simple, low VOC system, consisting of a liquid epoxy resin and an adducted cycloaliphatic diamine. The following objectives were targeted:
- Develop chemistries to improve barrier properties to chloride ion migration, the key contributor to corrosion in harsh environments.
- Impart attributes that provide flexibility and impact resistance to a system that has neither of these.
- Provide attributes to maintain or improve adhesion
- Invent functionality that will improve pot life and cure time
- The additive must also enhance aesthetics such as gloss or color.
- No added VOC’s
– Gerald Vandezande